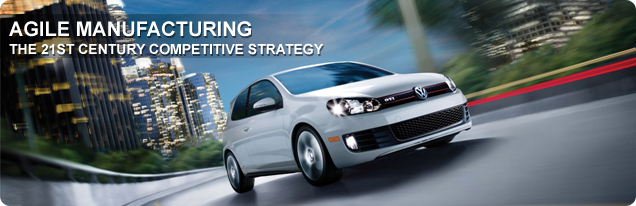
AGILE MANUFACTURING
To become an agile manufacturer, a company must recognize change in the marketplace and then manage and master that change. This section describes the market conditions that are pushing manufacturers toward adopting an agile manufacturing approach.
The Customer Has Changed
Today¡¯s customers focus on unique products and expect one-to-one marketing. As a result, they are less willing to accept mass-marketed goods and are rejecting one-size-fits-all products. This means that manufacturers must adapt and adopt the make-to-order mentality displayed by Japanese manufacturers in the 1980s in order to become customer-focused and supply customized products and services designed to match a particular customer profile.
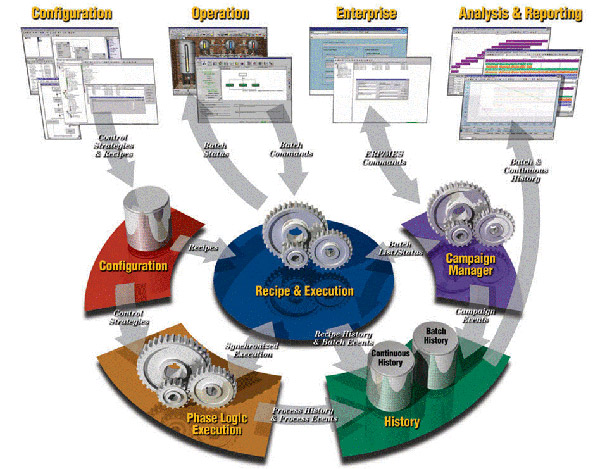
The Customer Relationship Has Changed
Customers expect personalization in their supply-chain relationships and best practices from their supply-chain partners. Manufacturers that can offer a more personalized relationship to their customers and confirm their use of world-class practices will survive. Those that cannot will lose their competitive edge and, eventually, lose customers and even whole markets. Even brand awareness, traditionally the linchpin of customer loyalty, is becoming less important than the ability to execute and meet customer needs.
Partnering Is the Name of the Game
Just-in-time (JIT) manufacturing practices have made it essential for manufacturers and their business partners, both customers and suppliers, to work more closely together. Customers need to participate in the product planning or system integration process, and suppliers need to take more responsibility for quality control or even manage inventory on behalf of the manufacturers. Refocusing on core competencies means that manufacturers are more likely to outsource to supply chain partners and become part of virtual teams that are focused on delivering a specific service or product.
E-business Is Changing Market Dynamics
The Internet has opened up a worldwide market to every manufacturer, and it has enabled customers to source products and services from any supplier, anywhere. Internet trading hubs and online marketplaces have created a significant amount of price transparency and are forcing more suppliers to meet the market in terms of their pricing and delivery. The Internet is increasing the visibility of supply chains and enabling virtual collaboration across supply chains, which are dramatically speeding up supply chain execution.
The Global Market Has Become a Reality
Today¡¯s companies can move into new marketplaces more easily than ever before because there are now fewer political and tariff borders. Trading blocks have emerged, such as NAFTA (North American Free Trade Agreement) and the European Union (EU), that facilitate international trade. Meanwhile, Asia and China represent massive emerging markets for absorbing manufacturing capacity and the Internet makes buying and selling across the globe relatively easy.
Product Know-how Is Key
Products that require a low level of know-how to manufacture cannot survive in high-wage countries, and standardized products that require little know-how will move to low-wage countries. Delivering products that require higher levels of know-how to produce is key to the survival of manufacturers in the developed countries. Creating these kinds of products demands better knowledge management in terms of the production process, market demands and customer needs.
Technology Is Cheaper, Faster and Better
As the pace of technological innovation continues to accelerate, technology is becoming cheaper, faster and better. Manufacturers of all types and levels have access to technology that can help them to respond faster and operate from smaller plants, using more flexible production methods. Complex manufacturing resource planning (MRP II) software has had its day. Today¡¯s manufacturing software is more flexible and easier to set up and use than traditional material requirements planning (MRP) applications and better able to support agile manufacturing.
Managing Change
The characteristics of an agile manufacturer include the following four ways of managing change:
•Recognition
•Focus on the customer
•Leveraging resources
•Cooperating to compete
The first step in managing change is to recognize that it is happening and proactively engage in change management. Companies can reexamine their markets and customers by looking for opportunities and risks. They can develop a planned change schedule as well as conducting a what-if exercise to prepare for unplanned change. They can also conduct a company-wide knowledge audit to determine what they are aware of and use the knowledge that is in their business systems, processes and employees.
Instead of allowing change to control your business, focusing on improving the customer¡¯s experience can be another way to control it. Customers want solutions that comprise both products and services and they require product flexibility and variability to meet their demands, as well as a quick response to any questions that relate to pricing and support.
An agile enterprise can also be recognized by its ability to successfully exploit its resources. It does not have idle capacity or poorly used resources. Part of change management is to identify underutilized, unused or non-existent resources and take better advantage of them or bring them on board. Agile manufacturers make resources work in teams and share knowledge to optimize the flow and cooperation within the enterprise.
Finally, agile manufacturers change the way that they interact with their business partners so that they can compete more effectively through cooperation. Today¡¯s successful enterprise knows that it does not dictate market demands: it listens to its customers. It finds its core competence and makes partnerships when it is necessary to provide the customer with a solution. Supply chain cooperation is only one aspect of becoming more cooperative¡ªknowledge sharing is another. A competitive company is a company looking for partners to benefit its own products and services.
Mastering Change
For manufacturers, mastering change involves a strategic realignment that is supported by the implementation of a number of tactical initiatives. The strategic realignment is to focus manufacturing systems and resources on supporting the business goal, rather than the traditional goal of controlling the plant or the manufacturing process. If the business goal is to respond faster to customer demands or to increase the breadth or depth of solutions provided, then the manufacturing systems and the resources they manage must be focused on this strategic objective.
The first tactical initiative is to do everything possible to reduce inventory levels. This is achieved in three ways:
•Eliminate waste
•Cut down transport time
•Reduce setup time
Eliminating waste improves the efficiency of supplying goods and services. Reducing transport times shortens both lead times and the timeframe needed for demand planning so that anticipated demand is not based on long-term assumptions. Reducing setup allows the production of smaller batches. As inventory represents both a risk and an investment, it is vital to keep inventory levels as low as possible without harming customer service.
Once inventory levels have been minimized, the manufacturer should focus on maximizing the throughput of the plant. Manufacturers should base production and distribution on current constraints and bottlenecks in the company (or in the supply chain) in order to maximize the throughput in the company.
While optimal throughput depends on many things (such as the physical layout of the plant and its production lines or work centers), it also depends on efficient supply chain collaboration. Efficient supply chain collaboration requires making the interaction between supply chain participants easier and faster, making supply chain processes more visible to the participants and encouraging an exchange of knowledge in the chain. Manufacturers need to ensure that they work with business partners that are good at providing products and (certain) services.
Where supply chain resources cannot be used to deliver a product or service, the manufacturer must ensure that individual employees and teams are properly empowered to fulfill their roles in the manufacturing process. This requires effective knowledge management: getting the most out of employees by empowering them to act and by increasing their skills, and by giving them the ability to find and use knowledge easily in their work.
Establishing cross-functional teams cuts down on middle management, and collaboration between employees in different areas of the plant motivates those employees to focus on improving the workflow. The company¡¯s business goals and its manufacturing processes will become transparent to the individuals and teams that are responsible for delivering and executing them.
AGILE MANUFACTURING SOFTWARE
Software that supports agile manufacturing is different from the manufacturing planning and control systems (for example, MRP) of the past. It is less about control and more about flexibility ¨C less about complex and deep functionality and more about programs that are easier to set up and use. Agile manufacturing focuses less on the process of manufacturing and more on the need to respond to customer demands.
How Is Agile Manufacturing Different from MRP?
Traditional software has often been geared toward giving the company strict control of all processes. The term manufacturing planning and control was coined to describe this business approach. Each area of the plant was measured separately. However, in retrospect, one can question how much value this control added to businesses.
Today, small and mid-size manufacturers are moving beyond the MRP II paradigm. While MRP II is still used, customers have recognized the need to adjust faster to market demands and to optimize business processes.
To quote manufacturing expert Brian Maskell, author of Software and the Agile Manufacturer, ¡°When MRP II and other systems taking the operations-research approach were being widely introduced into Western manufacturing industries, it was considered that adding features and functions improved a system. The best systems were the ones with the most ¡®bells and whistles.¡¯ In recent years this view has changed. Simpler systems, which do not burden the user with all kinds of subtle new features are easier to use and thus more effective. Well-designed simple systems are more useful than a system with all manners of detailed complexities.¡±
There is ample material documenting the failure of traditional manufacturing systems. For example, it is estimated that only 58% of all MRP II installations are successfull, and only 8% have achieved a positive improvement in performance from their ERP implementation.
The biggest asset for a manufacturing solution today is simplicity and flexibility. Instead of being a system that forces the manufacturer into workflows that don¡¯t match their business, they need to stay agile.
» More Information